In modern manufacturing, increasing emphasis is placed on a technically flawless surface. The constantly growing demands for ever lower surface roughness and a higher bearing ratio of the surfaces present tool development with ever new challenges. In addition, the process to be used should be as cost-effective and fast as possible.
The roller burnishing process meets all these requirements and achieves in a very short time what was previously only possible in lengthy and environmentally harmful processes, such as honing. In many respects, there are even more advantages that are not immediately apparent at first glance.
Decisive for the success of roller burnishing are parameters such as roller pressure and the rotational speed of the roller burnishing tool. When looking through a microscope and observing the roughness profile, one often gets the impression that the "peaks" are merely bent downwards by the burnishing rollers - a misconception.
Because the secret to the success of roller burnishing technology lies precisely in the material flow. The compressive stress at the point of contact between the WENAROLL roller burnishing tool and the workpiece surface is so great that exceeding the material's yield strength causes plastic deformation. This causes the roughness peaks to be pressed down almost perpendicular to the surface and the roughness valleys to be raised from below by the resulting material flow.
Figure 1 gives an impression of the process sequence and the resulting surface. The working speed, in turn, depends on the material used and the required surface values. Figures 2 and 3 show a cylindrical workpiece before and after roller burnishing, as well as the corresponding roughness measurements.
- Surfaces with a quality of Rz < 1 µm
- Fits can be produced reliably, quickly and cost-effectively
- Only one work operation required
- Long tool life and long service life of wearing parts
- The rolled surfaces are work-hardened, making them more resistant to wear
- Non-cutting and virtually noiseless machining
- Only one tool required, no additional costs
- Can be used on all rotary machining machines (CNC and conventional)
- Requires little cooling, can be operated with any cooling system
- Improvement of tribological properties
- Increase in fatigue strength
- Reduction of roughness by up to 70%
The machining allowance tolerance of the components before roller burnishing is equal to the pre-machined roughness depth (Rz). Since the roughness depth almost completely disappears during the process, the diameter of the components will decrease or increase by this amount. The initial roughness can, depending on the material, be between Rz = 5 µm and Rz = 50 µm.
Since the roughness after roller burnishing strongly depends on the initial roughness, a pre-machining process that is acceptable in terms of time should be selected. Graph 2 gives an impression of the residual roughness remaining after roller burnishing. The illustration shows that the remaining residual roughness is only a fraction of the original roughness.
WENAROLL roller burnishing tools can be used individually on lathes, milling machines (CNC and conventional), machining centers, transfer lines and special machines. Materials with a hardness of up to 45 HRC can be machined.
Depending on the requirements, WENAROLL roller burnishing tools machine cylindrical bores (through and blind), cylindrical shafts (continuous and stepped) as well as flat surfaces just as easily and quickly as conical internal and external surfaces.
Some examples of workpieces where high surface quality is important:
- Oil pumps and valve seats
- Connecting rods
- Bearing seats
- External surfaces of shafts
- Internal surfaces of hydraulic cylinders
- Surface of ball joints
- Internal and external conical seats of valve bodies
- Gas taps, pistons, gear parts, clutch parts, etc.
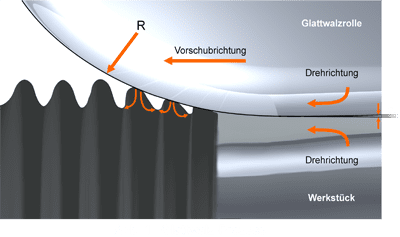
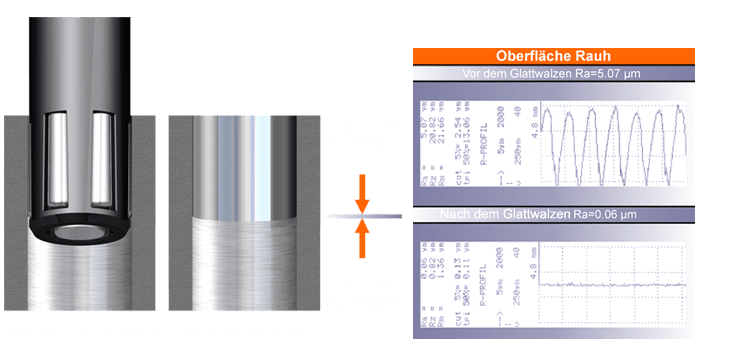